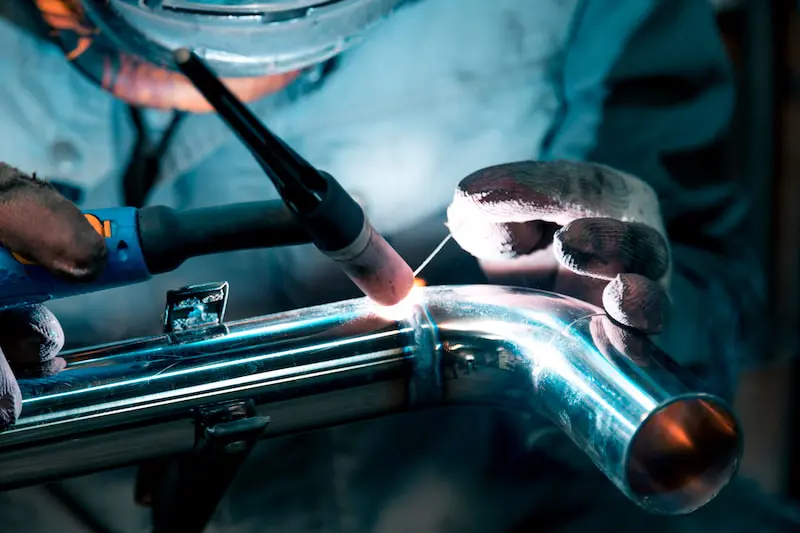
تأثیر جوشکاری بر استحکام و سختی فلزات
جوشکاری میتواند تأثیرات متفاوتی بر استحکام و سختی فلزات داشته باشد که به نوع فلز، روش جوشکاری، پارامترهای حرارتی و شرایط خنک شدن بستگی دارد. برخی از مهمترین تأثیرات آن عبارتاند از:
۱. کاهش استحکام در اثر تغییرات ریزساختاری
در حین جوشکاری، ناحیهای به نام منطقه متأثر از حرارت (HAZ) تحت دمای بالا قرار میگیرد. این حرارت میتواند باعث رشد دانههای فلزی و تغییر فازهای ریزساختاری شود که در برخی موارد استحکام فلز را کاهش میدهد.
۲. افزایش سختی و شکنندگی در برخی آلیاژها
در برخی فلزات مانند فولادهای کربنی و آلیاژی، جوشکاری میتواند باعث ایجاد مارتنزیت در منطقه جوش یا HAZ شود که منجر به افزایش سختی و در نتیجه شکنندگی میشود. اگر این سختی بیشازحد باشد، احتمال ترکخوردگی افزایش مییابد.برای اطلاع از لیست قیمت ورق استیل 316 با ما تماس بگیرین.
۳. تنشهای پسماند و اثر آن بر استحکام
جوشکاری باعث انبساط و انقباض در نواحی مختلف فلز میشود که تنشهای پسماند را به دنبال دارد. این تنشها ممکن است استحکام موضعی را کاهش داده و باعث ترکهای داخلی یا کاهش مقاومت در برابر بارگذاری شود.
۴. کاهش استحکام در فولادهای عملیات حرارتی شده
فولادهایی که تحت عملیات حرارتی خاصی مانند کوئنچ و تمپر قرار گرفتهاند، در اثر جوشکاری ممکن است خواص بهینه خود را از دست بدهند و نیاز به عملیات حرارتی مجدد داشته باشند تا استحکام اولیه بازگردد.
۵. وابستگی استحکام و سختی به روش جوشکاری
روشهای مختلف جوشکاری تأثیرات متفاوتی بر خواص مکانیکی دارند. مثلاً جوشکاری TIG معمولاً استحکام بالاتری را حفظ میکند، در حالی که جوشکاری قوس الکتریکی ممکن است منجر به تغییرات شدیدتر در سختی و استحکام شود.برای اطلاع از لیست قیمت ورق استیل 304 با ما تماس بگیرین.
راههای کاهش اثرات منفی جوشکاری بر استحکام و سختی
- انتخاب فیلر متناسب با فلز پایه برای کاهش ناهماهنگی در خواص مکانیکی
- استفاده از پیشگرم و عملیات تنشزدایی پس از جوشکاری برای کاهش ترکخوردگی
- کنترل میزان ورودی حرارت برای جلوگیری از رشد بیشازحد دانهها
- انتخاب روش جوشکاری مناسب بسته به نوع فلز و کاربرد موردنظر
با رعایت این نکات، میتوان تأثیرات منفی جوشکاری بر استحکام و سختی فلزات را به حداقل رساند و از کاهش خواص مکانیکی جلوگیری کرد.
منطقه متأثر از حرارت (HAZ) و تغییرات ریزساختاری
منطقه متأثر از حرارت (HAZ) و تغییرات ریزساختاری در جوشکاری
منطقه متأثر از حرارت (Heat Affected Zone – HAZ) یکی از مهمترین بخشهای قطعات جوشکاریشده است که بین فلز جوش و فلز پایه قرار دارد. این ناحیه مستقیماً تحت تأثیر حرارت جوشکاری قرار میگیرد اما ذوب نمیشود. در نتیجه، تغییرات ریزساختاری و مکانیکی در آن رخ میدهد که میتواند بر عملکرد نهایی قطعه تأثیر بگذارد.
۱. بخشهای مختلف HAZ
منطقه متأثر از حرارت بسته به میزان دمای اعمالشده و سرعت خنک شدن به چند بخش تقسیم میشود:
- منطقه دانههای درشت (Coarse-Grained HAZ):
نزدیکترین بخش به حوضچه جوش است و دمای بسیار بالایی را تجربه میکند. دانههای فلزی در این ناحیه رشد کرده و ممکن است استحکام کاهش یابد و شکنندگی افزایش یابد. - منطقه دانههای ریز (Fine-Grained HAZ):
دمای متوسطی دریافت میکند و ساختار دانهها در این ناحیه نسبتاً ریز و پایدارتر است. خواص مکانیکی معمولاً متعادلتر است. - منطقه بیندانهای (Intercritical HAZ):
در این ناحیه، بخشی از فلز فازهای مختلفی را تجربه میکند که میتواند باعث کاهش استحکام یا تغییر در سختی شود. - منطقه تحت تأثیر کم (Subcritical HAZ):
کمترین تأثیر حرارتی را دریافت کرده و تغییرات ساختاری جزئی است. ممکن است تنشهای پسماند در این ناحیه ایجاد شود.
۲. تغییرات ریزساختاری در HAZ
- رشد دانهها:
در دماهای بالا، دانههای فلزی رشد میکنند که باعث کاهش استحکام و افزایش شکنندگی میشود. - تشکیل مارتنزیت در فولادها:
اگر سرعت خنک شدن بالا باشد، ممکن است فاز مارتنزیتی شکل بگیرد که سخت ولی شکننده است. - رسوبزایی کاربیدها در فولادهای زنگنزن:
در برخی فولادهای زنگنزن، کاربید کروم در مرز دانهها رسوب میکند که باعث کاهش مقاومت به خوردگی بیندانهای میشود. - نرم شدن برخی آلیاژها:
در فولادهای سختکاریشده، گرمای جوشکاری میتواند باعث کاهش سختی و استحکام شود.
۳. راهکارهای کاهش اثرات منفی HAZ
- استفاده از پیشگرم و پسگرم برای کنترل سرعت خنک شدن و جلوگیری از ترکهای ناشی از تنشهای پسماند.
- انتخاب الکترود و فیلر مناسب که تطابق خوبی با فلز پایه داشته باشد.
- کنترل میزان ورودی حرارت برای جلوگیری از رشد بیشازحد دانهها.
- استفاده از عملیات حرارتی پس از جوشکاری (PWHT) برای بازگرداندن خواص مکانیکی.
منطقه HAZ یکی از چالشهای مهم در جوشکاری است و شناخت تغییرات آن میتواند به بهبود کیفیت جوش و حفظ خواص مکانیکی قطعه کمک کند.
نقش تنشهای پسماند در کاهش استحکام فلزات جوشکاریشده
نقش تنشهای پسماند در کاهش استحکام فلزات جوشکاریشده
تنشهای پسماند (Residual Stresses) یکی از اثرات نامطلوب جوشکاری هستند که میتوانند تأثیر منفی بر استحکام و عملکرد قطعات جوشکاریشده داشته باشند. این تنشها ناشی از تغییرات دمایی و انبساط و انقباض غیر یکنواخت در حین جوشکاری هستند و در صورت عدم کنترل، ممکن است منجر به ترکخوردگی، کاهش استحکام و کاهش طول عمر قطعه شوند.
۱. علت ایجاد تنشهای پسماند در جوشکاری
در فرآیند جوشکاری، حرارت بالا باعث انبساط موضعی در ناحیه جوش و منطقه متأثر از حرارت (HAZ) میشود. پس از سرد شدن، این مناطق دچار انقباض شده و به دلیل محدودیتهایی که از طرف فلزات اطراف وجود دارد، تنشهای پسماند ایجاد میشوند.برای اطلاع از لیست قیمت لوله استیل صنعتی با ما تماس بگیرین.
عوامل مؤثر در ایجاد تنشهای پسماند:
- گرادیان دمایی بالا در حین جوشکاری
- تفاوت در نرخ انبساط و انقباض فلزات مجاور
- سرد شدن سریع و نامتعادل
- روش جوشکاری و میزان ورودی حرارت
۲. تأثیر تنشهای پسماند بر استحکام فلزات جوشکاریشده
- افزایش احتمال ترکخوردگی ناشی از تنش (SCC):
وجود تنشهای کششی در نواحی جوشکاریشده باعث افزایش حساسیت به ترکخوردگی ناشی از تنش، مخصوصاً در محیطهای خورنده میشود. - کاهش مقاومت در برابر بارگذاری دینامیکی:
تنشهای پسماند ممکن است باعث کاهش مقاومت قطعات در برابر بارهای متناوب و در نتیجه ایجاد ترکهای خستگی شود. - اعوجاج و تغییر شکل قطعه:
توزیع نامناسب تنشهای پسماند میتواند باعث تغییر شکل قطعات و کاهش دقت ابعادی آنها شود. - کاهش چقرمگی شکست:
در برخی آلیاژها، تنشهای کششی پسماند میتوانند موجب کاهش مقاومت در برابر شکست و افزایش شکنندگی شوند.
۳. روشهای کاهش و کنترل تنشهای پسماند در جوشکاری
- پیشگرم کردن قطعه قبل از جوشکاری:
این روش باعث کاهش گرادیان حرارتی و کاهش تنشهای ناشی از انقباض میشود. - استفاده از الکترود و فیلر مناسب:
انتخاب مواد مناسب میتواند باعث کاهش تفاوت در انبساط و انقباض و در نتیجه کاهش تنشهای پسماند شود. - تنشزدایی حرارتی (PWHT):
یک روش مؤثر برای آزادسازی تنشهای پسماند، انجام عملیات حرارتی پس از جوشکاری است که باعث بازآرایی ساختاری و توزیع یکنواختتر تنشها میشود. - روشهای مکانیکی مانند چکشکاری و لرزش دادن قطعه:
این روشها به بهبود توزیع تنشها و کاهش تنشهای کششی کمک میکنند. - کنترل سرعت سرد شدن:
جلوگیری از سرد شدن ناگهانی با استفاده از روشهایی مانند عایقبندی حرارتی، از ایجاد تنشهای پسماند شدید جلوگیری میکند.
“تنشهای پسماند در جوشکاری میتوانند استحکام فلزات را کاهش داده و باعث مشکلاتی مانند ترکخوردگی، کاهش مقاومت در برابر خستگی و اعوجاج شوند. با استفاده از روشهای مناسب مانند پیشگرم کردن، تنشزدایی حرارتی و کنترل فرآیند جوشکاری، میتوان اثرات منفی این تنشها را کاهش داد و استحکام و عملکرد قطعات جوشکاریشده را بهبود بخشید.”برای اطلاع از لیست قیمت لوله استیل صنایع غذایی با ما تماس بگیرین.
ترکخوردگی و شکنندگی در اثر جوشکاری
ترکخوردگی و شکنندگی در اثر جوشکاری
جوشکاری به دلیل اعمال حرارت و تنشهای موضعی میتواند باعث ایجاد ترکخوردگی و افزایش شکنندگی در فلزات شود. این مشکلات در اثر تغییرات ریزساختاری، انبساط و انقباضهای حرارتی، و تنشهای پسماند به وجود میآیند و در صورت عدم کنترل، ممکن است منجر به کاهش استحکام و خرابی زودهنگام قطعه شوند.
۱. انواع ترکخوردگی در جوشکاری
ترکهای جوشکاری به دو دسته کلی تقسیم میشوند: ترکهای گرم که در حین جوشکاری یا بلافاصله پس از آن ایجاد میشوند و ترکهای سرد که پس از خنک شدن و در اثر تنشهای داخلی یا عوامل محیطی ظاهر میشوند.
الف) ترکهای گرم (Hot Cracks)
این نوع ترکها هنگام انجماد فلز جوش و در دماهای بالا رخ میدهند. معمولاً در اثر انقباض شدید حین انجماد و ترکیب شیمیایی نامناسب جوش ایجاد میشوند. بیشتر در آلیاژهایی مانند فولادهای زنگنزن، آلومینیوم و نیکل دیده میشوند.برای اطلاع از لیست قیمت لوله استیل پزشکی با ما تماس بگیرین.
دلایل ترکهای گرم:
- وجود گوگرد و فسفر که باعث تشکیل ترکیبات شکننده میشوند.
- اختلاف زیاد در نرخ انقباض فلز پایه و فلز جوش.
- استفاده از حرارت بیش از حد که منجر به رشد بیشازحد دانهها و کاهش استحکام میشود.
ب) ترکهای سرد (Cold Cracks)
این ترکها پس از خنک شدن جوش، معمولاً در دمای اتاق یا حتی چند روز بعد ظاهر میشوند. عمدتاً در فولادهای کربنی و آلیاژی رخ میدهند و اغلب به ترکخوردگی هیدروژنی مربوط میشوند.
دلایل ترکهای سرد:
- نفوذ هیدروژن در فلز جوش که باعث شکنندگی و ترکخوردگی میشود.
- تنشهای پسماند بالا که در اثر انبساط و انقباض غیر یکنواخت ایجاد میشوند.
- ساختار مارتنزیتی در منطقه متأثر از حرارت (HAZ) که شکننده است.
۲. شکنندگی در اثر جوشکاری
شکنندگی جوش میتواند ناشی از عوامل مختلفی باشد که منجر به کاهش چقرمگی و افزایش احتمال شکست میشوند.
مهمترین عوامل شکنندگی:
- تشکیل مارتنزیت سخت و شکننده در فولادهای پرکربن در اثر سرد شدن سریع.
- رسوبزایی نامطلوب کاربیدها که باعث کاهش انعطافپذیری میشود.
- ایجاد تنشهای کششی پسماند که تمایل به شکست را افزایش میدهد.
- ورود ناخالصیهایی مانند گوگرد و فسفر که نواحی ضعیف و مستعد ترکخوردگی را ایجاد میکنند.
۳. روشهای پیشگیری از ترکخوردگی و شکنندگی در جوشکاری
پیشگرم کردن فلز پایه باعث کاهش سرعت سرد شدن و جلوگیری از تشکیل مارتنزیت شکننده میشود.
انتخاب الکترود و فلز پرکننده مناسب به کاهش تشکیل فازهای ترد کمک میکند.
کاهش میزان هیدروژن در جوش از طریق استفاده از الکترودهای خشک و کنترل میزان رطوبت در محیط جوشکاری میتواند از ایجاد ترکهای سرد جلوگیری کند.
کنترل ورودی حرارت با تنظیم شدت جریان و سرعت جوشکاری از رشد بیشازحد دانهها و ایجاد ساختار شکننده جلوگیری میکند.
استفاده از عملیات تنشزدایی پس از جوشکاری (PWHT) به کاهش تنشهای پسماند و جلوگیری از ترکخوردگی کمک میکند.
طراحی مناسب اتصال جوشکاری و توزیع مناسب تنشها احتمال ایجاد ترک را کاهش میدهد.
تأثیر جوشکاری بر مقاومت به خوردگی فلزات
تأثیر جوشکاری بر مقاومت به خوردگی فلزات
جوشکاری میتواند تأثیر چشمگیری بر مقاومت به خوردگی فلزات داشته باشد. در فرآیند جوشکاری، تغییرات دمایی شدید، تغییرات ریزساختاری و تنشهای پسماند باعث ایجاد نواحی مستعد خوردگی میشوند. در صورتی که جوشکاری بهدرستی انجام نشود، ممکن است مقاومت به خوردگی فلز کاهش یافته و عمر مفید قطعه کوتاهتر شود.
۱. عوامل مؤثر بر کاهش مقاومت به خوردگی در اثر جوشکاری
چندین عامل میتوانند موجب کاهش مقاومت به خوردگی در فلزات جوشکاریشده شوند:
- تغییرات ریزساختاری: جوشکاری باعث تغییر در ترکیب شیمیایی و توزیع عناصر آلیاژی در منطقه جوش و منطقه متأثر از حرارت (HAZ) میشود که ممکن است منجر به کاهش مقاومت در برابر خوردگی گردد.
- تنشهای پسماند: در اثر انبساط و انقباض حین جوشکاری، تنشهای پسماند ایجاد میشود که میتواند باعث افزایش حساسیت به خوردگی تنشی (SCC) شود.
- ناخالصیها و آلودگیها: ورود اکسیژن، نیتروژن و ناخالصیهایی مانند سولفیدها به داخل فلز جوش، احتمال تشکیل فازهای نامطلوب و کاهش مقاومت به خوردگی را افزایش میدهد.
- ناهمگنی ترکیب شیمیایی: ترکیب شیمیایی در ناحیه جوش و اطراف آن ممکن است با فلز پایه تفاوت داشته باشد که موجب افزایش احتمال خوردگی گالوانیکی بین فلز جوش و فلز پایه میشود.
۲. انواع خوردگی در جوشکاری
خوردگی در قطعات جوشکاریشده میتواند به اشکال مختلفی رخ دهد که مهمترین آنها شامل موارد زیر هستند:
الف) خوردگی بیندانهای (Intergranular Corrosion)
این نوع خوردگی معمولاً در فولادهای زنگنزن رخ میدهد. در دمای بالا، کروم موجود در فولاد با کربن ترکیب شده و کاربیدهای کروم در مرزدانهها رسوب میکنند. این مسئله باعث تخلیه کروم از نواحی اطراف شده و مقاومت به خوردگی آن قسمت کاهش مییابد.
ب) خوردگی حفرهای (Pitting Corrosion)
در صورت وجود نواقص سطحی در جوش، مانند ترکهای ریز و حفرهها، محلهای مستعد خوردگی موضعی ایجاد میشوند. این نوع خوردگی بهویژه در محیطهای کلریدی (مانند آب دریا) شدیدتر است.
ج) خوردگی گالوانیکی (Galvanic Corrosion)
اگر فلز جوش و فلز پایه ترکیب شیمیایی متفاوتی داشته باشند، یک سلول گالوانیکی تشکیل شده و ناحیه دارای پتانسیل الکتروشیمیایی پایینتر دچار خوردگی میشود.
د) خوردگی تنشی (Stress Corrosion Cracking – SCC)
ترکیب تنشهای پسماند و محیط خورنده میتواند موجب ترکخوردگی و شکست زودهنگام قطعات شود. این نوع خوردگی معمولاً در فولادهای زنگنزن و آلیاژهای نیکل رخ میدهد.
۳. روشهای کاهش اثرات منفی جوشکاری بر مقاومت به خوردگی
برای جلوگیری از کاهش مقاومت به خوردگی در اثر جوشکاری، باید از روشهای زیر استفاده کرد:
- انتخاب الکترود و فلز پرکننده مناسب: استفاده از مواد جوشکاری که دارای ترکیب شیمیایی سازگار با فلز پایه باشند، احتمال خوردگی گالوانیکی را کاهش میدهد.
- کنترل ورودی حرارت: جلوگیری از حرارت بیش از حد در حین جوشکاری باعث کاهش رسوب کاربیدهای کروم و کاهش احتمال خوردگی بیندانهای میشود.
- عملیات حرارتی پس از جوشکاری (PWHT): انجام عملیات حرارتی مناسب، مانند آنیل کردن محلول، میتواند باعث حل شدن رسوبات مضر و بهبود مقاومت به خوردگی شود.
- پسیو کردن (Passivation): استفاده از فرآیندهای شیمیایی برای بازسازی لایه اکسید محافظ بر سطح فولادهای زنگنزن میتواند مقاومت به خوردگی را افزایش دهد.
- تمیزکاری و پرداخت سطحی: حذف اکسیدها، سربارهها و ناخالصیهای سطحی از جوش، احتمال ایجاد نقاط مستعد خوردگی را کاهش میدهد.
- استفاده از پوششهای محافظ: اعمال پوششهای ضدخوردگی مانند رنگ، گالوانیزه و پوششهای نیکل میتواند مقاومت به خوردگی را افزایش دهد.
“جوشکاری میتواند مقاومت به خوردگی فلزات را کاهش داده و منجر به خرابی زودهنگام قطعات شود. با انتخاب روشهای جوشکاری مناسب، کنترل ترکیب شیمیایی، استفاده از عملیات حرارتی پس از جوشکاری و رعایت استانداردهای تمیزکاری، میتوان از این مشکلات جلوگیری کرده و عمر مفید سازههای جوشکاریشده را افزایش داد.”
راهکارهای کاهش اثرات منفی جوشکاری بر خواص مکانیکی فلزات
راهکارهای کاهش اثرات منفی جوشکاری بر خواص مکانیکی فلزات
جوشکاری میتواند تأثیرات منفی بر خواص مکانیکی فلزات بگذارد. برای کاهش این اثرات، چندین راهکار مؤثر وجود دارد که در ادامه به بررسی آنها پرداختهایم.
انتخاب صحیح روش جوشکاری
روش جوشکاری تأثیر زیادی بر کیفیت جوش و خواص مکانیکی آن دارد. روشهایی مانند جوشکاری قوسی با گاز محافظ (GTAW) یا جوشکاری لیزری به دلیل تأثیر حرارتی کم، میتوانند اثرات منفی را کاهش دهند و جوشهایی با استحکام بالاتر تولید کنند.
کنترل ورودی حرارت
کنترل ورودی حرارت یکی از عوامل مهم در کاهش تغییرات ریزساختاری و تنشهای پسماند است. تنظیم دقیق پارامترهایی مانند شدت جریان، ولتاژ و سرعت جوشکاری میتواند از گرم شدن بیش از حد و تشکیل ساختارهای ناخواسته جلوگیری کند.
پیشگرم کردن فلز پایه
پیشگرم کردن قطعات فلزی قبل از جوشکاری، بهویژه در فولادهای پرکربن و آلیاژی، میتواند از تشکیل فازهای شکننده و کاهش تنشهای پسماند جلوگیری کند. این عمل باعث میشود که جوش با کیفیت بالاتری بهدست آید.
استفاده از الکترود و مواد پرکننده مناسب
انتخاب فلز پرکننده مناسب با توجه به ترکیب شیمیایی فلز پایه اهمیت زیادی دارد. مواد پرکننده با خواص مکانیکی مشابه یا بهتر از فلز پایه میتوانند استحکام و چقرمگی جوش را بهبود بخشند و احتمال ایجاد نواحی ضعیف را کاهش دهند.
کاهش و کنترل تنشهای پسماند
تنشهای پسماند میتوانند منجر به ترکخوردگی و کاهش استحکام جوش شوند. برای کنترل این تنشها، استفاده از عملیات حرارتی مانند تنشزدایی پس از جوشکاری، به ویژه در دماهای مناسب، میتواند به کاهش تنشهای پسماند کمک کند. همچنین، استفاده از طراحی مناسب برای اتصالات جوشکاری میتواند توزیع یکنواخت تنشها را تسهیل کند.برای اطلاع از لیست قیمت لوله استیل 316 با ما تماس بگیرین.
استفاده از روشهای جوشکاری پیشرفته
روشهای نوین جوشکاری مانند جوشکاری لیزری یا جوشکاری قوسی زیرپودری میتوانند به کاهش تغییرات ریزساختاری، افزایش سرعت جوشکاری و کاهش خطر تشکیل فازهای ترد کمک کنند. این روشها به دلیل دقت بالاتر در فرآیند، جوشهای با کیفیت بهتری تولید میکنند.
استفاده از پوششهای محافظ قبل از جوشکاری
پوششهای محافظ میتوانند از آلودگی سطحی و نفوذ عناصر مضر مانند اکسیژن یا نیتروژن جلوگیری کنند. این پوششها به حفظ ترکیب شیمیایی فلز جوش و جلوگیری از تشکیل نواحی ضعیف کمک میکنند و در نتیجه خواص مکانیکی جوش بهبود مییابد.
عملیات حرارتی خاص (سختکاری و آنیلکاری)
پس از جوشکاری، انجام عملیات حرارتی میتواند باعث بهبود خواص مکانیکی جوش شود. سختکاری میتواند استحکام و سختی جوش را افزایش دهد، در حالی که آنیلکاری میتواند به کاهش تنشهای پسماند و بهبود انعطافپذیری و چقرمگی جوش کمک کند.
استفاده از تکنیکهای بازسازی جوش
در برخی موارد، ممکن است جوش دچار مشکلاتی مانند ترکهای داخلی یا ضعف در استحکام شود. در این مواقع، بازسازی جوش و انجام مجدد فرآیند جوشکاری میتواند کیفیت جوش را بهبود بخشد و خواص مکانیکی را بازسازی کند.
اجرای آزمونهای کنترل کیفیت جوش
برای اطمینان از کیفیت جوش و خواص مکانیکی آن، باید از آزمونهای غیرمخرب مانند رادیوگرافی و التراسونیک استفاده کرد. همچنین انجام آزمونهای مخرب مانند کشش، ضربه و سختیسنجی میتواند به ارزیابی دقیقتر استحکام و چقرمگی جوش کمک کند.برای اطلاع از لیست قیمت لوله استیل 310 با ما تماس بگیرین.
شبیهسازی فرآیند جوشکاری
با استفاده از مدلهای شبیهسازی رایانهای میتوان رفتار جوش و توزیع حرارت و تنشها را پیشبینی کرد. این مدلها به مهندسان کمک میکنند تا پارامترهای جوشکاری را بهینهسازی کنند و از بروز مشکلات مکانیکی جلوگیری کنند.
این راهکارها بهویژه زمانی مؤثر هستند که در طراحی و اجرای فرآیند جوشکاری به دقت رعایت شوند. به کارگیری این روشها باعث کاهش تأثیرات منفی جوشکاری بر خواص مکانیکی فلزات و تولید جوشهایی با کیفیت بالا خواهد شد.برای اطلاع از لیست قیمت لوله استیل 304 با ما تماس بگیرین.