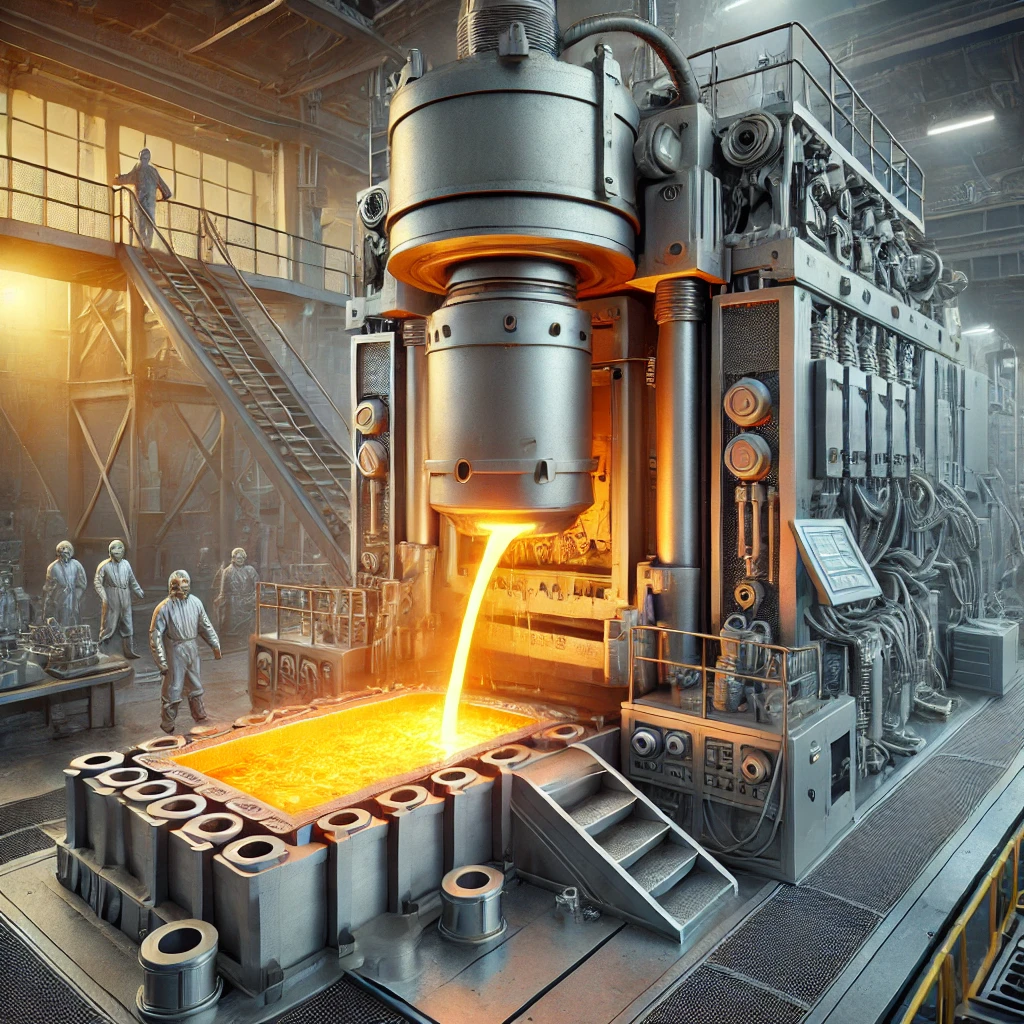
مفهوم ریختهگری تحت فشار (Die Casting)
ریختهگری تحت فشار یا Die Casting یکی از فرآیندهای ریختهگری است که در آن فلز مذاب تحت فشار بالا به درون یک قالب فلزی (Die) وارد میشود. این روش به طور معمول برای تولید قطعات پیچیده و دقیق با حجم زیاد مورد استفاده قرار میگیرد. در این فرآیند، فلز با فشار زیاد به داخل قالب ریخته میشود، که باعث میشود ذرات فلزی به شکل دقیقتری شکل بگیرند و ویژگیهایی مانند مقاومت و دقت ابعادی بالا حاصل شود. این فرآیند به دلیل سرعت بالای تولید و دقت بالا، در صنایع مختلفی از جمله خودروسازی، الکترونیک، و لوازم خانگی کاربرد گستردهای دارد.
در ریختهگری تحت فشار، دو نوع قالب معمولاً استفاده میشود: قالبهای فولادی برای تولید قطعات فلزی دقیق و قالبهای آلومینیومی که برای تولید قطعات با وزن سبکتر مناسب هستند. این قالبها معمولاً از دو بخش اصلی تشکیل شدهاند: قالب ثابت و قالب متحرک. وقتی فلز مذاب وارد قالب میشود، تحت فشار بالا قرار گرفته و به سرعت داخل قالب پخش میشود. پس از سرد شدن و سفت شدن فلز، قالب باز شده و قطعه نهایی از آن خارج میشود.
یکی از ویژگیهای برجسته ریختهگری تحت فشار، توانایی تولید قطعات با ویژگیهای دقیق ابعادی است. در این روش، فشار زیاد موجب میشود که فلز مذاب به راحتی درون قالب جریان یابد و تمام جزئیات دقیق قالب را پر کند. این ویژگی باعث میشود که قطعات تولید شده به دقت بالایی برسند و نیاز به عملیات تکمیلی کمتری داشته باشند. همچنین، این روش به کاهش هدررفت مواد کمک میکند و باعث میشود که قطعات با نسبت هزینه به کارایی بالاتری تولید شوند.
فرآیند ریختهگری تحت فشار معمولاً در دو نوع اصلی انجام میشود: ریختهگری تحت فشار افقی و ریختهگری تحت فشار عمودی. در روش افقی، قالبها در جهت افقی قرار دارند و فلز مذاب به داخل قالب تحت فشار وارد میشود. در روش عمودی، قالبها به صورت عمودی قرار دارند و این روش معمولاً برای قطعات کوچکتر و با دقت بیشتر مناسب است. هر یک از این روشها ویژگیها و کاربردهای خاص خود را دارند و بر اساس نوع قطعه و نیازهای تولید انتخاب میشوند.
این فرآیند از نظر هزینههای انرژی و زمان تولید نسبت به بسیاری از روشهای دیگر ریختهگری بسیار بهینه است. در ریختهگری تحت فشار، سرعت تولید بالا است و میتواند هزاران قطعه مشابه در مدت زمان کوتاه تولید کند. به همین دلیل، این روش برای تولید انبوه قطعات با ابعاد کوچک و متوسط بسیار مناسب است. همچنین، ریختهگری تحت فشار میتواند تولید قطعاتی با سطوح صاف و بدون نقص را امکانپذیر سازد.
ریختهگری تحت فشار برای تولید قطعاتی که به دقت ابعادی بالا، سطوح صاف و مقاومت مکانیکی زیاد نیاز دارند، انتخابی ایدهآل است. این فرآیند میتواند با استفاده از انواع مختلف فلزات مانند آلومینیوم، روی، مس، و آهن انجام شود و در صنایع خودروسازی، هوافضا، الکترونیک، لوازم خانگی و بسیاری از صنایع دیگر کاربردهای گستردهای دارد.
مزایا و معایب ریختهگری تحت فشار
ریختهگری تحت فشار (Die Casting) یکی از روشهای بسیار محبوب برای تولید قطعات فلزی است که به دلیل مزایای فراوان در صنایع مختلف کاربرد دارد. این روش، به ویژه در مقایسه با سایر روشهای ریختهگری مانند ریختهگری گرانشی و ریختهگری ماسهای، ویژگیهایی دارد که آن را به انتخاب اول برای تولید قطعات با دقت بالا و نیاز به تولید انبوه تبدیل کرده است. با این حال، مانند هر روش دیگری، این روش نیز معایب خاص خود را دارد که باید قبل از انتخاب آن در نظر گرفته شود.برای اطلاع از لیست قیمت لوله استیل صنعتی با ما تماس بگیرین.
مزایای ریختهگری تحت فشار
- دقت ابعادی بالا و کیفیت سطحی عالی یکی از بزرگترین مزایای ریختهگری تحت فشار، توانایی تولید قطعات با دقت ابعادی بسیار بالا است. به دلیل فشار زیاد که فلز مذاب به قالب وارد میکند، جزئیات قالب به طور کامل پر میشود و قطعه نهایی دارای سطح صاف و بدون نقص است. این ویژگی باعث کاهش نیاز به عملیات تکمیلی مانند ماشینکاری و پرداخت میشود که در بسیاری از روشهای دیگر ریختهگری ضروری است.
- تولید انبوه با سرعت بالا ریختهگری تحت فشار به دلیل سرعت بالای تولید، برای تولید قطعات انبوه بسیار مناسب است. فرآیند این روش میتواند در مدت زمان کوتاهی هزاران قطعه مشابه تولید کند، که این ویژگی برای صنایعی که نیاز به تولید سریع و در مقیاس بزرگ دارند، بسیار ارزشمند است. همچنین، به دلیل کاهش زمان تولید، هزینههای تولید نیز به طور قابل توجهی کاهش مییابد.
- استفاده بهینه از مواد اولیه در ریختهگری تحت فشار، به دلیل فشار زیاد، فلز مذاب به طور کامل داخل قالب پخش میشود و هدررفت مواد بسیار کم است. این ویژگی باعث میشود که نسبت به بسیاری از روشهای دیگر ریختهگری، بهرهوری مواد بالاتر باشد و هزینههای مواد اولیه کاهش یابد. این امر به ویژه در تولید قطعات پیچیده که نیاز به دقت بالا دارند، اهمیت زیادی پیدا میکند.
- قابلیت تولید قطعات پیچیده و دقیق ریختهگری تحت فشار توانایی تولید قطعات پیچیده و دقیق را با جزئیات زیاد فراهم میکند. این روش میتواند قطعاتی با اشکال هندسی پیچیده، سوراخها و ویژگیهای دقیق تولید کند که در بسیاری از روشهای دیگر به دشواری قابل تولید هستند. این ویژگی باعث میشود که ریختهگری تحت فشار برای صنایعی مانند خودروسازی و الکترونیک که نیاز به قطعات دقیق و پیچیده دارند، بسیار مناسب باشد.
معایب ریختهگری تحت فشار
- هزینه بالای قالبها یکی از معایب اصلی این روش، هزینه بالای قالبها است. قالبهای مورد استفاده در ریختهگری تحت فشار معمولاً از فولاد سخت ساخته میشوند که به دلیل نیاز به دقت بالا و استحکام، هزینه بالایی دارند. این موضوع باعث میشود که برای تولید تعداد کم قطعه، استفاده از این روش اقتصادی نباشد و ممکن است روشهای دیگر مانند ریختهگری گرانشی یا ماسهای گزینه بهتری باشند.
- محدودیت در انتخاب مواد ریختهگری تحت فشار محدودیتهایی در انتخاب مواد اولیه دارد. این روش عمدتاً برای فلزات با نقطه ذوب پایین مانند آلومینیوم، روی و منیزیم مناسب است. برای فلزات با نقطه ذوب بالا، مانند فولاد و آهن، این روش کمتر کاربرد دارد. این محدودیت میتواند در صنایعی که نیاز به استفاده از فلزات خاص دارند، مشکلساز باشد.
- پتانسیل برای نقصهای تولید در حالی که ریختهگری تحت فشار مزایای زیادی دارد، اما میتواند در مواردی منجر به تولید قطعات معیوب شود. مشکلاتی مانند تجمع گاز در قالب، انقباض فلز و تشکیل حبابهای هوا میتواند باعث ایجاد نقصهای داخلی در قطعات شود. این موارد معمولاً نیاز به کنترل دقیق شرایط فرآیند و تنظیمات قالب دارند که در غیر این صورت میتواند باعث کاهش کیفیت تولیدات شود.
- محدودیتهای اندازه و ضخامت قطعه به دلیل فشار بالایی که در این روش به فلز اعمال میشود، تولید قطعات با ابعاد بسیار بزرگ یا ضخامتهای زیاد به دشواری صورت میگیرد. برای تولید قطعات بزرگتر، معمولاً از روشهای دیگر مانند ریختهگری گرانشی استفاده میشود. این محدودیتها میتواند باعث شود که ریختهگری تحت فشار برای برخی از انواع قطعات مناسب نباشد.
با توجه به مزایا و معایب ذکر شده، انتخاب ریختهگری تحت فشار بستگی به نیازهای خاص تولید، نوع قطعه و حجم تولید دارد. این روش برای تولید قطعات دقیق و انبوه بسیار مناسب است، اما هزینه بالای قالبها و محدودیتهای انتخاب مواد و اندازه قطعه ممکن است در برخی شرایط استفاده از آن را محدود کند.برای اطلاع از لیست قیمت ورق استیل 304 با ما تماس بگیرین.
انواع ریختهگری تحت فشار
ریختهگری تحت فشار (Die Casting) به دو دسته اصلی تقسیم میشود: ریختهگری تحت فشار عمودی و ریختهگری تحت فشار افقی. هر یک از این روشها ویژگیها و کاربردهای خاص خود را دارند و بر اساس نوع قطعه و نیازهای تولید انتخاب میشوند. در ادامه به بررسی این دو نوع پرداخته میشود.
- ریختهگری تحت فشار عمودی (Vertical Die Casting)
در روش ریختهگری تحت فشار عمودی، قالب به صورت عمودی قرار میگیرد و فلز مذاب از طریق فشار به درون قالب وارد میشود. در این روش، قالب به سمت پایین یا بالا حرکت نمیکند و جریان مذاب به طور مستقیم از بالا به داخل قالب میرود. این روش بیشتر برای قطعات کوچک، دقیق و پیچیده که نیاز به دقت ابعادی بالایی دارند، استفاده میشود.
یکی از مزایای ریختهگری تحت فشار عمودی، این است که به دلیل قرارگیری عمودی قالب، امکان کاهش نیاز به سیستمهای پیچیده و هزینههای اضافی برای مکانیزمهای حرکت قالب وجود دارد. همچنین این روش برای تولید قطعات با ویژگیهای خاص مانند سوراخهای داخلی یا بخشهای دقیق و پرجزئیات بسیار مناسب است. از جمله کاربردهای این روش میتوان به تولید قطعات الکترونیکی و قطعات کوچک صنعتی اشاره کرد.
این نوع ریختهگری معمولاً برای تولید قطعات کوچکتر از جنس آلومینیوم، روی و سایر فلزات نرم مورد استفاده قرار میگیرد. به دلیل فشار بالا و کنترل دقیق، قطعات تولیدی در این روش دارای دقت بالایی در ابعاد و سطح هستند.
- ریختهگری تحت فشار افقی (Horizontal Die Casting)
در روش ریختهگری تحت فشار افقی، قالب به صورت افقی قرار دارد و فلز مذاب تحت فشار به درون قالب وارد میشود. در این روش، قالب معمولاً به دو قسمت تقسیم میشود: یک قسمت ثابت و یک قسمت متحرک که به هنگام فرآیند ریختهگری بسته و باز میشود. این روش به دلیل طراحی افقی قالب، امکان تولید قطعات بزرگتر و پیچیدهتر را فراهم میکند و میتواند برای تولید قطعاتی با ابعاد متوسط تا بزرگ مناسب باشد.
ریختهگری تحت فشار افقی برای قطعاتی که نیاز به تولید سریع و در تعداد زیاد دارند، بسیار مناسب است. از آنجا که قالبهای افقی معمولاً برای تولید قطعات بزرگتری طراحی شدهاند، میتوان از این روش برای ساخت قطعات صنعتی و خودرویی، مانند بدنه موتورهای خودرو، قابها و سایر اجزای سنگین استفاده کرد.برای اطلاع از لیست قیمت ورق استیل 316 با ما تماس بگیرین.
این روش همچنین میتواند برای تولید قطعاتی با پیچیدگی متوسط، سوراخهای داخلی و ساختارهای توخالی مناسب باشد. برخلاف روش عمودی، در این روش نیاز به سیستمهای پیچیدهتری برای هدایت و کنترل فلز مذاب و خروج قطعات از قالب وجود دارد.
- تفاوتهای کلیدی بین ریختهگری عمودی و افقی
- جهت قالب: در ریختهگری عمودی، قالب به صورت عمودی قرار دارد و در ریختهگری افقی، قالب به صورت افقی قرار میگیرد.
- اندازه و پیچیدگی قطعات: ریختهگری افقی بیشتر برای تولید قطعات بزرگتر و پیچیدهتر استفاده میشود، در حالی که ریختهگری عمودی مناسب برای تولید قطعات کوچک و دقیق است.
- هزینه و زمان: ریختهگری عمودی معمولاً هزینه کمتری نسبت به ریختهگری افقی دارد، به دلیل ساختار سادهتر و نیاز به سیستمهای کمتر پیچیده.
- کاربردها: ریختهگری افقی بیشتر در تولید قطعات خودرویی و صنعتی بزرگ کاربرد دارد، در حالی که ریختهگری عمودی معمولاً برای قطعات الکترونیکی و دقیق استفاده میشود.
- انتخاب روش مناسب
انتخاب بین ریختهگری تحت فشار عمودی و افقی بستگی به نیازهای تولیدی دارد. اگر هدف تولید قطعات دقیق و کوچک باشد، روش عمودی انتخاب مناسبی است. از طرف دیگر، اگر نیاز به تولید قطعات بزرگتر و با پیچیدگیهای متوسط وجود داشته باشد، روش افقی ترجیح داده میشود. علاوه بر این، عواملی همچون هزینه قالب، سرعت تولید و نوع فلز مورد استفاده نیز میتوانند در انتخاب روش تأثیرگذار باشند.برای اطلاع از لیست قیمت ورق استیل صنعتی با ما تماس بگیرین.
هر دو روش دارای کاربردهای گستردهای در صنایع مختلف هستند و بسته به نیاز تولید، میتوان از آنها بهره برد. به طور کلی، ریختهگری تحت فشار در مقایسه با سایر روشهای ریختهگری به دلیل دقت بالا و تولید سریع قطعات انبوه، محبوبیت زیادی دارد.
کاربردهای ریختهگری تحت فشار
ریختهگری تحت فشار (Die Casting) به دلیل دقت بالا، سرعت تولید زیاد و توانایی تولید قطعات پیچیده، در بسیاری از صنایع مختلف کاربرد دارد. این روش بهویژه برای تولید قطعات فلزی دقیق و انبوه که نیاز به استحکام و کیفیت بالا دارند، انتخاب مناسبی است. در اینجا به بررسی برخی از صنایع و محصولاتی که از این روش بهره میبرند، پرداخته میشود.برای اطلاع از لیست قیمت ورق استیل پانچ با ما تماس بگیرین.
صنعت خودروسازی
یکی از بزرگترین صنایع مصرفکننده ریختهگری تحت فشار، صنعت خودروسازی است. در این صنعت، قطعاتی مانند بدنه موتور، چرخ دندهها، قابهای ترمز، سیستمهای تعلیق، و سایر اجزای پیچیده خودرو توسط این روش تولید میشوند. این قطعات به دقت ابعادی بالا، استحکام مکانیکی و سطح صاف نیاز دارند که ریختهگری تحت فشار بهخوبی از عهده آن برمیآید. همچنین، به دلیل سرعت بالای تولید، این روش برای تولید قطعات در مقیاس انبوه بسیار مناسب است.
صنعت الکترونیک
در صنعت الکترونیک، تولید قطعاتی مانند محفظههای دستگاههای الکترونیکی، اتصالات و اجزای داخلی کامپیوترها، و قطعات موبایل با استفاده از ریختهگری تحت فشار رایج است. این قطعات معمولاً نیاز به دقت بالا و کیفیت سطحی بینظیر دارند که ریختهگری تحت فشار قادر به تأمین آن است. بهویژه در ساخت محفظههای فلزی برای گوشیهای موبایل، تلویزیونهای هوشمند، و لوازم خانگی هوشمند، این روش کاربرد فراوانی دارد.
صنعت هوافضا
در صنعت هوافضا، ریختهگری تحت فشار برای تولید قطعات پیچیدهای که باید وزن کم و استحکام بالایی داشته باشند، استفاده میشود. قطعاتی مانند محفظههای موتور، سیستمهای سوخترسانی، و دیگر اجزای فلزی هواپیماها با استفاده از این روش تولید میشوند. در این صنعت، دقت و استحکام بسیار مهم هستند و ریختهگری تحت فشار میتواند قطعاتی با ویژگیهای مطلوب برای تحمل شرایط سخت هوافضا تولید کند.
صنعت لوازم خانگی
در صنعت لوازم خانگی، بسیاری از قطعات فلزی کوچک مانند دربهای یخچال، اجاقهای گاز، وسایل برقی، و موتورهای کوچک با استفاده از ریختهگری تحت فشار ساخته میشوند. این روش امکان تولید قطعات با کیفیت بالا و در زمان کوتاه را فراهم میآورد. قطعات تولیدی به دلیل دقت بالا و ظاهر صاف، به راحتی در فرآیند مونتاژ لوازم خانگی مورد استفاده قرار میگیرند.برای اطلاع از لیست قیمت ورق استیل دکوراتیو با ما تماس بگیرین.
صنعت پزشکی
در صنعت پزشکی، ریختهگری تحت فشار برای تولید قطعات کوچک و دقیق که در تجهیزات پزشکی مانند دستگاههای تصویربرداری، ابزارهای جراحی، و سیستمهای تشخیص پزشکی به کار میروند، مورد استفاده قرار میگیرد. این قطعات باید دارای ویژگیهایی مانند استحکام بالا، دقت ابعادی دقیق و تطابق با استانداردهای بهداشتی باشند که ریختهگری تحت فشار میتواند این نیازها را تأمین کند.
صنعت ابزارآلات و ماشینآلات
در صنعت ابزارآلات و ماشینآلات، از ریختهگری تحت فشار برای تولید قطعات دقیق و پیچیده مانند دندهها، بلبرینگها، پمپها و موتورهای کوچک استفاده میشود. این قطعات نیاز به تحمل فشارهای بالا، دوام طولانیمدت و دقت بالا دارند که ریختهگری تحت فشار قادر به تولید آنها با کیفیت مطلوب است. این روش میتواند تولید قطعاتی با ویژگیهای دقیق و سازگار با عملکرد دستگاهها را ممکن سازد.
صنعت بستهبندی و حمل و نقل
در صنعت بستهبندی و حمل و نقل، از ریختهگری تحت فشار برای تولید قطعات فلزی مانند قابهای باربری، اتصالات بستهبندی، و قطعات مربوط به سیستمهای حملونقل استفاده میشود. این قطعات به دلیل نیاز به استحکام و مقاومت بالا در برابر فشار و ضربه، بهطور معمول با استفاده از ریختهگری تحت فشار تولید میشوند. این روش میتواند در مقیاسهای بزرگ برای تولید قطعات متعدد و با کیفیت بالا مناسب باشد.
صنعت انرژی و نفت و گاز
در صنعت انرژی و نفت و گاز، ریختهگری تحت فشار برای تولید قطعاتی مانند موتورها، توربینها، پمپها، و سیستمهای هدایت جریان مورد استفاده قرار میگیرد. این قطعات نیاز به دقت و استحکام بالا دارند تا بتوانند در شرایط سخت محیطی و فشارهای بالا عملکرد مطلوبی داشته باشند. ریختهگری تحت فشار با تولید قطعات مقاوم و دقیق، این نیازها را بهخوبی برآورده میکند.برای اطلاع از لیست قیمت ورق استیل برش خورده با ما تماس بگیرین
با توجه به ویژگیهای خاص ریختهگری تحت فشار، این روش در صنایع مختلفی کاربرد دارد و میتواند به تولید قطعات دقیق، با کیفیت بالا و در زمان کوتاه کمک کند. از خودروسازی تا الکترونیک، هوافضا، لوازم خانگی، پزشکی و صنایع دیگر، این روش یکی از گزینههای محبوب برای تولید انبوه قطعات پیچیده و با دقت بالا است.
چالشها و پیشرفتهای تکنولوژی در ریختهگری تحت فشار
ریختهگری تحت فشار، با وجود مزایای زیادی که دارد، همچنان با چالشهای مختلفی مواجه است که بر کیفیت و کارایی این روش تأثیر میگذارند. در این بخش، به تحلیل این چالشها و پیشرفتهای جدید در تکنولوژی ریختهگری تحت فشار پرداخته خواهد شد که به بهبود کیفیت و کارایی این فرآیند کمک میکنند.برای اطلاع از لیست قیمت ورق استیل تاجدار با ما تماس بگیرین.
چالشها در ریختهگری تحت فشار
محدودیتهای ماده اولیه یکی از بزرگترین چالشها در ریختهگری تحت فشار، انتخاب ماده اولیه مناسب است. در این فرآیند، معمولاً از فلزات غیرآلیاژی مانند آلومینیوم، روی، مس، و منیزیم استفاده میشود، اما این مواد نمیتوانند همه ویژگیهای مورد نیاز برای تمامی کاربردها را فراهم کنند. بهویژه در صنایع حساس مانند هوافضا یا خودرو، ممکن است نیاز به استفاده از آلیاژهایی با ویژگیهای خاص باشد که مشکلاتی را در فرآیند ریختهگری ایجاد میکند.
آلودگی و نقصهای سطحی یکی دیگر از چالشها، وجود نقصهایی مانند حبابهای هوا، ترکها و آلودگیهای سطحی در قطعات تولیدی است. این نقصها میتوانند بهطور مستقیم بر کیفیت و استحکام قطعات تأثیر بگذارند. در ریختهگری تحت فشار، این مشکلات معمولاً ناشی از فرآیند تزریق مواد مذاب به قالب در فشار بالا است. مراقبتهای دقیق در کنترل دما، فشار و سرعت تزریق میتواند از بروز این مشکلات جلوگیری کند، اما در عمل این یک چالش مداوم است.
هزینههای بالای تجهیزات هزینههای بالای تجهیزات و قالبها در ریختهگری تحت فشار یکی دیگر از مشکلات عمده است. این روش نیازمند قالبهای دقیق و با کیفیت بالا است که تولید و نگهداری آنها هزینههای زیادی را به دنبال دارد. بهویژه برای تولید قطعات پیچیده یا با مقیاس کوچک، این هزینهها ممکن است غیرقابل توجیه باشد.
محدودیتهای طراحی برخلاف روشهای دیگر ریختهگری که میتوانند به راحتی قطعات با هندسههای پیچیدهتر را تولید کنند، ریختهگری تحت فشار معمولاً محدودیتهایی در طراحی قطعات دارد. به دلیل محدودیتهای فیزیکی قالبها و نیاز به استفاده از فشار بالا برای تزریق، طراحی قطعاتی با اشکال پیچیده یا دارای جزئیات بسیار کوچک میتواند چالشبرانگیز باشد.برای اطلاع از لیست قیمت ورق استیل بگیر با ما تماس بگیرین.
پیشرفتهای تکنولوژی در ریختهگری تحت فشار
استفاده از مواد جدید و پیشرفته یکی از پیشرفتهای مهم در ریختهگری تحت فشار، توسعه و استفاده از آلیاژهای جدید است که ویژگیهای بهتر و خاصتری را ارائه میدهند. تحقیقات مداوم در زمینه مواد جدید مانند آلیاژهای آلومینیوم و منیزیم با ویژگیهای بهبود یافته و آلیاژهای مقاوم به حرارت به این فرآیند کمک کردهاند تا بتوان قطعات مقاومتر و با کیفیت بالاتری تولید کرد.
پیشرفت در طراحی قالبها طراحی قالبها یکی از کلیدیترین بخشها در بهبود کیفیت فرآیند ریختهگری تحت فشار است. پیشرفتهای تکنولوژیکی در زمینه طراحی قالبها با استفاده از نرمافزارهای شبیهسازی سهبعدی، امکان بهینهسازی طراحی قالبها را فراهم کرده است. این نرمافزارها به مهندسان کمک میکنند تا پیش از ساخت واقعی قالب، عملکرد آن را شبیهسازی کرده و نقاط ضعف و مشکلات احتمالی را شناسایی کنند.
هوشمندسازی و کنترل فرآیند با استفاده از سیستمهای کنترل هوشمند و حسگرهای پیشرفته، فرآیند ریختهگری تحت فشار به دقت و کارایی بیشتری دست یافته است. این حسگرها به صورت لحظهای اطلاعاتی در مورد دما، فشار و سرعت تزریق ارائه میدهند و امکان تنظیم دقیق فرآیند را در اختیار اپراتورها قرار میدهند. این پیشرفتها به کاهش نقصهای تولید و بهبود کیفیت قطعات کمک میکنند.برای اطلاع از لیست قیمت ورق استیل شانه تخم مرغی با ما تماس بگیرین.
بهبود سیستمهای خنکسازی یکی از چالشهای رایج در ریختهگری تحت فشار، دمای بالای فلز مذاب و نیاز به خنکسازی سریع قالبها است. پیشرفتهای جدید در سیستمهای خنکسازی قالب، مانند استفاده از سیستمهای خنکسازی فعال و جریانهای سیال هوشمند، به بهبود کیفیت قطعات و کاهش زمان تولید کمک کردهاند. این سیستمها میتوانند دمای قالب را به طور یکنواخت و کنترلشده نگه دارند تا از بروز ترکها و نقصهای دیگر جلوگیری کنند.
روشهای پیشرفته برای کاهش هزینهها با توجه به هزینههای بالا در تولید قالبها و تجهیزات، پیشرفتهایی در زمینه ساخت قالبهای چندبار مصرف و استفاده از تکنیکهای قالبسازی سریع صورت گرفته است. این روشها میتوانند هزینههای تولید را کاهش دهند و امکان تولید قطعات پیچیدهتر و با دقت بالاتر را در مقیاسهای کوچک و متوسط فراهم کنند.
ارتقاء فرآیندهای پس از تولید پیشرفتهای تکنولوژیکی در زمینه پردازشهای پس از تولید مانند پرداخت سطح، ماشینکاری دقیق و پوششدهی به بهبود کیفیت قطعات تولیدی کمک کرده است. این فرآیندها میتوانند نقصهای سطحی یا ساختاری قطعات را اصلاح کنند و قطعاتی با کیفیت بهمراتب بالاتر تولید نمایند.برای اطلاع از لیست قیمت ورق استیل 316L با ما تماس بگیرین.
ریختهگری تحت فشار بهعنوان یک روش تولید پیشرفته و دقیق، با وجود چالشهای متعدد، همچنان در حال پیشرفت است. استفاده از مواد جدید، پیشرفت در طراحی قالبها، سیستمهای هوشمند کنترل فرآیند، و بهبود روشهای خنکسازی و پردازش پس از تولید، این صنعت را به سمت کارایی بالاتر و کیفیت بهتر هدایت کردهاند. همچنین، با کاهش هزینهها و بهبود دقت، ریختهگری تحت فشار همچنان یک انتخاب برجسته در صنایع مختلف باقی میماند.برای اطلاع از لیست قیمت ورق استیل 304L با ما تماس بگیرین.